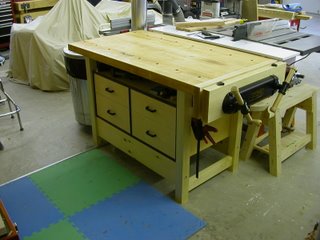
The Veritas Twin-Screw vise was a true pain to install. 8/4 Hard Maple is pretty heavy, especially when you have a 7-1/8" x 30" piece of it, then try swinging around 2 of these clamped together. When drilling the holes for the screws to go through I realized why I need a bigger drill press -- it is hard to drill a 3-1/2" deep hole with a drill press that only has 2-3/4" of quill movement. Stopping in the middle of each hole to move the table up wasn't much fun, then the table tilt bolt decided to loosen up and the table shifted. All in all, I'm amazed the holes came as close to parallel as they did. Attaching the back jaw to the table was very easy, the included bolts work like a charm. Attaching the screws to the back jaw also went very easy. Then came attaching the screws to the front vise, and bam! I sheared off one of the bolts that holds the vise screw in place. Did I overtighten it? No, the head was yet to touch any material in front of it, I was still about an 1/8" from the bolt being in place. I ended up drilling it out, plugging the hole, and using one of my own bolts. With the vise up and running, oh wait, the screws didn't want to turn, so it's up but not running... I loosened the bolts on one screw and it worked much better, guess those holes weren't as parallel as I thought. I just left the bolts slightly loose, it seems to work pretty well now.
This project entailed a couple firsts for me. The biggest was installing a bunch of real drawers. The drawers are made of 1/2" pine. I dovetailed the fronts to the sides, then put the back in with a sliding dovetail. The bottoms for the smaller top drawers are 1/4" mdf. The bottom drawers have 3/8" BC ply for bottoms.
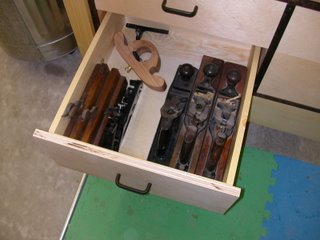
Building this bench was quite fun overall, and ended up being pretty cheap (other than the vise). The vise was $190 but is well worth it. I used the bench to build the drawers, and when cutting dovetails on long boards it is awesome to be able to just but it in the middle and slide it down close to the jaw. I ended up using Rockler plastic bench dogs, 4 for $3.99, instead of the more expensive veritas ones. I haven't been able to try out the Veritas ones, but I think they would be a big improvement.